Low-chemical Maine home for myalgic encephalomyelitis patient
Excerpt from Pretty Good House: A Guide to Better Homes shows how a new home became a refuge from unhealthy building materials and other environmental hazards.
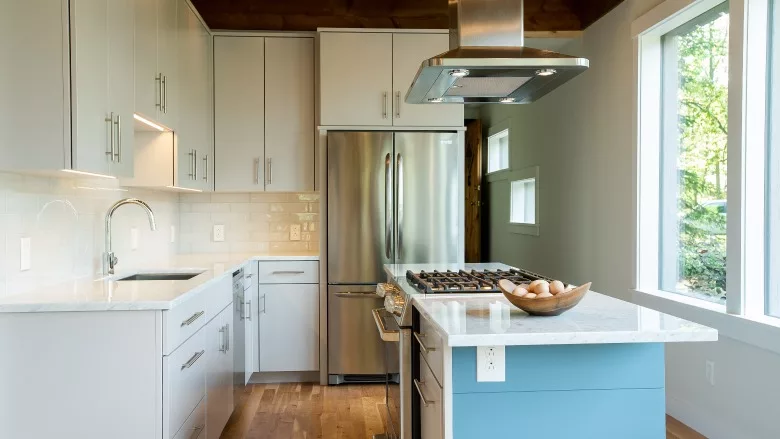
The following case study is an except from the new book from construction authors Dan Kolbert, Emily Mottram, Michael Maines and Christopher Briley. The study focuses on one new home in Maine. It was designed not as an architectural tour de force, but as a refuge from unhealthy building materials and other environmental hazards.
The owner's health problems, which began while she lived near a bus station in Boston, were originally attributed to mold, environmental toxins such as petroleum, and a virus. Jill was eventually diagnosed with myalgic encephalomyelitis, and her sensitivity to chemical fumes, pollution, and other environmental hazards prompted her to look for a healthier place to live.
Jill and her mother began traveling to possible locations where they counted the number of cars that went by, a barometer of how clean the air should be. In Oxford County, Maine, some 125 miles to the north, they found a wooded lot where little traffic passed. “I think they had one or two cars in an hour,” says architect Emily Mottram. “They’re remote but still in a good school district for her two children.”
The location was half of it. They also needed a house that offered similar advantages, and that meant cutting adhesives and plastics wherever possible. A good start was finding Jesse Stacy, a builder who already was using board sheathing and flooring rather than plywood or oriented strand board.
“That was normal practice for him,” Mottram says. “It wasn’t more expensive or complicated. Their whole house smelled like pine boards while they were building it. It was absolutely wonderful.”
As Mottram and Stacy selected materials and components for the house, Mottram would sometimes ask for samples and scraps—a baggie of cellulose insulation, a bit of gypsum drywall, a piece of Romex electrical cable. She’d box them up and send them to the owner to see if any of the material prompted a reaction. The strategy was to eliminate all possible plastic, adhesives, and potential chemical irritants until no further cuts were practical. Flooring and trim came unfinished; kitchen cabinets were built by a local shop, made with solid wood, and painted with zeroVOC paints. The siding is wood, and Mottram used metal roofing instead of asphalt shingles. The owner went so far as to buy a soy-based release agent for the concrete forms. Mechanical ventilation took care of whatever irritants might have remained in the air.
Mottram makes no claims of architectural grandeur in this compact 1,400-sq.-ft. home. Originally planned as a simple 24-ft.-by-24-ft. two-story box at roughly 1,150 sq. ft., it grew slightly with the addition of a one-car garage and a 14-ft.-by-14-ft. first-floor primary bedroom that the owner’s mother could use in the future. The full bath on the first floor will give the house aging-in-place potential.
The double-stud wall design, whose exterior walls and vaulted ceiling are insulated with dense-pack cellulose, is heated with ductless mini-split heat pumps and ventilated with a Broan ERV. The meticulous attention to detail paid off. Mottram urged the owner to stay mostly away from the job site until the house could be completed and thoroughly cleaned. Since move-in, Jill has experienced no sensitivity problems. But she has enjoyed the views of the White Mountains in the distance. “It’s an absolutely perfect spot,” says Mottram. “They really lucked out.”
Keeping Indoor Air Healthy
Most kitchen cabinets are made with panel goods that contain some type of adhesive. Even when drawer fronts and face frames are solid lumber, cabinet boxes are typically made from particleboard or plywood whose fibers are bonded together with glue—and the glue can be an issue for people with extreme chemical sensitivities. The problem can be minimized if not eliminated by finding a cabinetmaker who works with solid wood throughout and uses low- or zero-VOC paints and finishes to complete the work, as local cabinet maker Henry Banks did for this home. The same logic can be applied to trim and flooring. In this case, those products came unfinished and were finished on site with products like Vermont Natural Coatings.