Efficient installation of contaminant vapor barrier restores project schedule at expansive logistics center
The MonoShield contaminant vapor barrier system was designed to meet these sites' fast-paced demands and dynamic environments

Aerial view of logistics center construction. Courtesy from Land Science
A new logistics center at a former brownfield site in New Jersey is being redeveloped to provide valuable warehouse space to the Northeast region. Its industrial location required that vapor intrusion (VI) be addressed as a preemptive measure and a contaminant vapor barrier comprising thin-mil plastic sheeting was initially specified. From the start, the highly problematic installation caused serious scheduling delays and before the first warehouse was completed, the developer began searching for a VI prevention alternative that would fully protect future building occupants and regain control of the project schedule.
Installation of Thin-Mil Plastic Vapor Barrier Causes Scheduling Woes
The planned logistics center, located in the heart of a long-established industrial corridor between New York and Philadelphia, would serve one of the world’s densest population bases and help meet the growing demand for warehouse capacity in the region.
The development team initially opted to install a 20-mil plastic vapor barrier that utilized tape. This vapor barrier met the requirements in the construction specification and was originally thought to provide the lowest-cost alternative for addressing VI.
The installation of the thin-mil plastic barrier at the first building was slow-moving from the start, and the concrete pour schedule was delayed multiple times. The reasons for the delays were twofold: first, taping the vapor barrier together was a labor-intensive process, and second, the thin mil plastic barrier was not durable enough to hold up against ongoing construction activities, which would continue to jeopardize the barrier’s integrity.
Moreover, because the thin-mil vapor barrier was continuously damaged, punctured, and pulled out of place, it could not pass the quality control/quality assurance (QA/QC) testing (i.e., smoke testing) required by the design engineer’s specification.
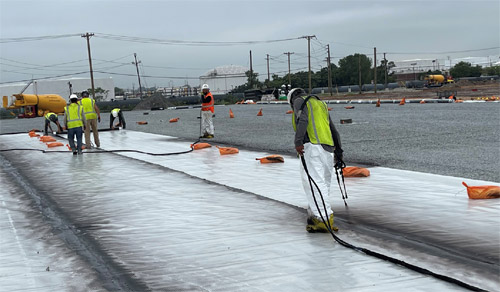
Developer Turns to Experienced VI Installation Contractor with New Solution
After numerous delays and continuous repairs to the thin mil plastic vapor barrier, the development team adjusted course, contracting one of the region’s most experienced VI mitigation system (VIMS) installation specialists and an Engineering-News Record (ENR) Top 100 General Contractors (GCs) & Developer, to safeguard the remaining buildings of the large-scale development.
A leading factor in the decision to change course was the contractor's experience with installing a contaminant vapor barrier utilizing a metalized film technology that was purposefully engineered to provide a high level of protection against vapor intrusion while improving installation efficiency at large warehouse developments. In recent years, the company has installed millions of square feet of this vapor barrier technology at new warehouse construction sites.
The MonoShield contaminant vapor barrier system was designed to meet these sites' fast-paced demands and dynamic environments by providing more efficient constructability over high-density polyethylene (HDPE) and superior chemical and puncture resistance compared to thin-mil plastic vapor barriers.
MonoShield DescriptionThe MonoShield vapor barrier is a 30-mil composite geomembrane comprised of a chemically resistant metalized film encased in polyethylene low-permeance, flexible polymers, and a reinforcing grid bonded to a geotextile on the underside. A unique spray-applied nitrile-modified asphalt latex is used to seal the seams, utility penetrations, and perimeter terminations, offering 10x greater chemical resistance than conventional spray-applied asphalt latex materials contained in other systems. The barrier's puncture-resistant, reinforced geotextile fabric is engineered to withstand typical construction job site traffic. Together, these components form a barrier that is chemically resistant, significantly improves installation efficiency, and maintains integrity throughout the installation process. |
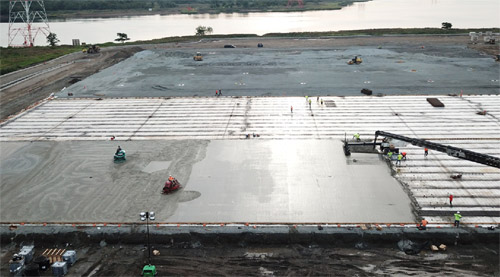
Implementation: MonoShield Vapor Barrier, Installed by a Certified Applicator, Improves Productivity while Increasing Protection from Vapor Intrusion
The contractor, an experienced Certified Applicator trained by the manufacturer, took over the project, beginning with the second building, where MonoShield was installed in strict accordance with the manufacturer's specifications.
Smoke testing was regularly conducted during the installation per the manufacturer’s quality assurance/quality control (QA/QC) specifications. A Certified Inspector oversaw the smoke testing and observed and documented that MonoShield was correctly installed throughout the project.
Moreover, the Land Science-certified installer efficiently coordinated with the General Contractor and concrete subcontractor to achieve a streamlined installation process backed by the manufacturer's technical support provided throughout the project. Cumulatively, these factors contributed to a VI protection solution with improved chemical resistance, durability, and productivity in the field, giving the development team peace of mind in its investment.
Results and Conclusion
Due to its ease of installation and the contractor’s expertise as a Certified Applicator, MonoShield's installation time was cut in half compared to the thin-mil plastic vapor barrier initially used for the project. This change in direction quickly realigned the project, accelerating the concrete pour schedule and yielding significant time and cost savings for the project overall.
Over three million square feet of warehouse space are now protected by MonoShield at this major logistics center development. Its advanced metalized film and nitrile-modified asphalt components ensure a high level of VI protection for building occupants against any residual contamination that may be present in the subsurface.
Supported by MonoShield, the new logistics center generates many new employment opportunities, transforming a large, vacant brownfield into a catalyst for economic vibrancy in the region.